“Friction and sealing" Laboratory
Objectives:
The laboratory deals with the problems associated with static and dynamic sealing devices. In particular, experimental and numerical analysis are carried out on pneumatic single seals and components, evaluating friction forces, wear, durability and sealing efficiency.
Alcuni progetti:
- Friction force measurement in seals and actuators
- Radial force and contact pressure measurement on seals
- Contact pressure measurement on seals
- Accelerated life test on pneumatic cylinders an seals
- Non-conventional sealing systems for low-friction pneumatic cylinders
- Visualization of seals deformed geometry
Friction force measurement in seals and actuators
Guido Belforte, Luigi Mazza, Andrea Manuello
A test bench for friction forces measurement was designed and manufactured as a modular system.
Tests are allowed on:
- A whole commercial cylinder;
- A couple of piston-seals or single piston-seal, mounted on a suitable equipment and sliding inside a cylinder bore;
- A rod seal, mounted on a second suitable equipment;
- A valve spool-seal.
The figure shows the manufactured test bench, assembled in the configuration for measuring friction force on a commercial cylinder. An electrocylinder drives with constant velocity the rod of the cylinder under test; the friction force due to relative motion is discharged on the cylinder barrel supported by an air bearing pad and measured by a load cell.
G. Belforte, A. Manuello Bertetto, L. Mazza, “Test rig for friction force measurements in pneumatic components and seals”,Proc. of IMechE, Part J:Journal of Engineering Tribology,227, 1, pp 43-59, (2013).
G. Belforte, M. Conte, A. Manuello, L. Mazza, “Performance and behavior of seals for pneumatic spool valves”, Tribology Transactions,54, pp. 237-246, (2011).
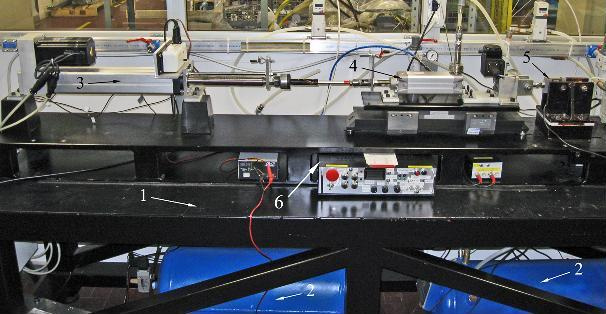
Radial force and contact pressure measurement on seals
Guido Belforte; Andrea Manuello Bertetto; Luigi Mazza; Terenziano Raparelli; Carmen Visconte
A test bench was designed and manufactured for an indirect measurement of the contact pressure between a lip seal for pneumatic cylinder rod and the counterpart.
The radial force is acquired in time, while the seal is pulled on a sensorised rod at slow and constant velocity by a linear actuator. Contact pressure distribution is worked out deriving the acquired signal. In order to ensure no additional friction during the measurement except seal friction, pneumostatic bearings and pads were provided.
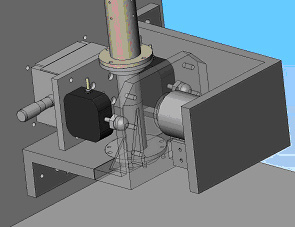
Contact pressure measurement on seals
Guido Belforte, Luigi Mazza, Carmen Visconte, Andrea Manuello Bertetto
An experimental procedure for measuring contact pressure between a pneumatic seal and its counterface was developed. In particular, measurements can be performed using pressure sensitive films, to be interposed between the contact surfaces. Tests can be carried out both on a seal rectilinear specimen and on various commercial piston seals, varying pressure load and lubrication.
With reference to tests on piston seals (F = 50 mm), a commercial pneumatic cylinder was modified and used as test rig. A window was manufactured on the cylinder bore, so that a film sensor sheet could be placed upon the seal.
Belforte G, Conte M, Manuello Bertetto A, Mazza L, Visconte C., Experimental and numerical evaluation of contact pressure in pneumatic seals, Tribology International, 42(1), pp. 169-175, (2009).
Accelerated life test on pneumatic cylinders an seals
Guido Belforte, Luigi Mazza, Carmen Visconte, Andrea Manuello Bertetto
Experiment analysis performed to evaluate cylinders life the wear resistance of the guide bearing and. Tests can be carried out on cylinders subjected to radial load in conditions very similar to what established by standards or under more severe operating conditions (accelerated life tests). The methodology specifies cylinders supply pressure, compressed air filtration conditions, rod velocity entity of the load applied to the rod and cylinder greasing conditions.
A device was designed and manufactured in order to measure the radial thickness of worn material on the sealing edge, by means of a laser sensor, without contact and without disassembling the seals.
Manuello, L. Mazza, P. Orrù, “Contact pressure distribution in guide bearings for pneumatic actuators”, Experimental Techniques, doi:10.1111/ext.12014, (2013).
G. Belforte, L. Mazza, C. Visconte, “Non contact wear measurement on pneumatic seals”,Tribology International, 48, pp. 73-77, (2012).
G. Belforte, A. Manuello Bertetto, L. Mazza, P.F. Orrù “Life prediction of guide bearings for linearpneumatic actuators”,2nd European Conference on Tribology – ECOTRIB 2009, Pisa, Italy, (2009).
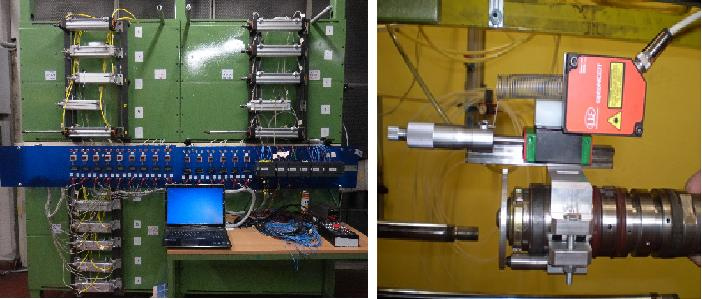
Non-conventional sealing systems for low-friction pneumatic cylinders
Guido Belforte, Terenziano Raparelli, Luigi Mazza, Carmen Visconte, Andrea Trivella
This activity deals with lip seals with a non-conventional mounting on the piston in order to obtain a simple controlled-leakage system that reduces friction forces in pneumatic cylinders economically and effectively. The non-conventional mounting consists of positioning the lip seal in the direction opposite to that used in a conventional installation, so that the contact pressure reduces as air pressure in the chamber rises. In this way, an air gap is created at the sliding interface which allows air in the pressurized chamber to escape past the seal lip, thus reducing the contact force on the barrel. The piston is provided with a hole which exhausts the leakage flow to the atmosphere. Both commercial spring-loaded lip seal and special prototype are studied.
T. Raparelli, L. Mazza, A. Trivella, “Non-conventional lip seal mountings for pneumatic cylinders”,European Conf. onTribology ECOTRIB 2015, Lugano, Switzerland, 3-5 June 2015.
G. Belforte, L. Mazza, C. Visconte, “Design methodology for an air lubricated seal”,Tribology International, 75, pp. 104-110, (2014).
T. Raparelli, L. Mazza, A. Trivella, “Study of a non-conventional sealing system for low-friction pneumatic cylinders,inProc. of4thInt. Conf. on Tribology and Design, Kos, Greece, 3-5 September 2012.
Visconte C.; Conte M; Mattone M.C, “Analysis of the leakage pathin an air-lubricated seal”, Tribology International,42(6), pp. 844-848, (2009)
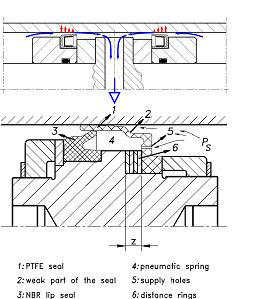
Visualization of seals deformed geometry
Guido Belforte, Andrea Manuello Bertetto, Luigi Mazza
A test bench was designed and manufactured allowing the optical visualization of seals cross section deformation. This bench makes it possible to assess seal deformation and any extrusion that may occur while varying seal installation and operating conditions. In particular, seal operating pressure, material, seat geometry and the clearance between the seat and the sliding surface can all be changed independently. In this way, it was also possible to develop black box models for predicting the behaviour of different types of seal.
C. Bignardi, A. Manuello, L. Mazza, “Photoelastic Measurements and Computation of the Stress Field and Contact Pressure in a Pneumatic Lip Seal”,Tribology International, 32, pp. 1-13, (1999)
T. Raparelli, A. Manuello Bertetto, L. Mazza "Experimental Study of Pneumatic Seal Extrusion",Tribology Transaction, 40, 4, pp. 715-719, (1997)
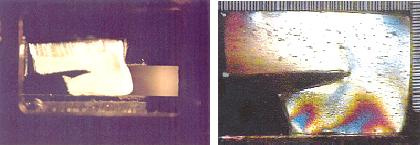